The Coming Transition from Traditional Hardware Displays to Electronic Screens for Train Control
Train control systems interface to operators via a device which communicates signal aspects, speeds and provide various system information in texts and graphics. Different suppliers and systems use various names for such devices such as aspect display unit (ADU) or cab display unit (CDU). In the past 20 years, there has not been significant technological change in these devices. Many are still being installed with toggle switches, manual push buttons and light arrays in trains across North America.
In the rest of the world, however, train control human machine interfaces (HMIs) have changed significantly in the past years, with many systems transitioning to TFT screens with buttons and, more recently, full touch screen technology like ones used on smart phones.
While this evolution has an obvious aesthetic appeal, the primary advantages of migrating to software-driven devices boil down to lower life-cycle costs and additional functional capabilities.
The older style HMIs contain many subcomponents – all of which must be wired together, often by hand. Deployments are sometimes a project-specific application with – for example – screen masks being custom silkscreened for each customer or application. This customization adds cost. Utilizing a software-driven display allows for a standardized hardware approach while decoupling functionality from hardware. Together, this makes the initial hardware deployment much less costly.
Life-cycle costs are also impacted in other ways. Beyond the upfront material cost improvements, the design flexibility provides for relatively easy modifications. Oftentimes, systems are changed after they have been placed in service. With traditional hardware-based HMI devices, changes to applications in the field can take years to deploy. Design modifications must be laid out and wiring and panels modified in the field or replaced entirely. For larger fleets, this is a lengthy effort and necessitates running mixed operations (with both the old and new configurations) for a considerable period of time. Software-based panels reduce the entire process time down to weeks. Software upgrades can be installed on dozens of trains per day with no hardware modifications required at all. Mixed fleet running is minimized, and the total cost of executing changes is a fraction of that associated with hardware-based devices.
The functional capabilities of these newer devices are also significant. Multiple screens can be shown on the same hardware, allowing for the provision of diagnostic or maintenance data, messaging, etc. Graphics or even photos can be used to provide context, mimicking the HMI designs seen in other industrial areas such as automation and the automotive field. This can greatly improve the human factor or “cognitive ergonomics” of system design and improve operational reliability and safety.
Importantly, displayed screens, operator selections and actions can be recorded with software-based devices. This allows for important post-incident investigations and can greatly improve operator training and operational rule making design.
Both input and output functions can achieve a SIL2/3 safety level with modern devices. While most traditional hardware-based train control HMIs are not considered “fail-safe”, some do include functions which are. Being able to replicate that level of safety with software can be an important cost savings.
Maybe most importantly, as smart phones and tablets have forced almost everyone to interface with touchscreen technology, there is less objection and mistrust than in the past. Most users have a familiarity with the technology in their everyday lives.
These are among the reasons why Europe and Asia have largely transitioned to software-driven train control HMIs - a trend that is also well established in many other areas from industrial automation to the automotive environment. With such significant advantages, why has the technology not been widely adopted in North America?
Signaling and train control systems are often the most conservative and slowly evolving subsystems (such software displays are already used for TCMS, CCTV, etc.). People who are not familiar with using such electronics will often first question its robustness. In fact, the newer screens are more durable than hardwired devices. Capable of operating at temperatures so extreme no human operator can be expected to be present, one device type currently in service is reporting field mean time between failure values exceeding 600,000 hours, which equates to approximately 70 years. With the latest optical bonding technology, and the removal of physical keys, these devices are even more incredibly robust and reliable.
Another concern in the early years of deployment was screen brightness and the ability to read displays accurately in various light conditions. Modern train control displays offer a brightness in excess of 1,000 nits and automatically detect and adjust brightness based on ambient light sensors (just like a smartphone).
Cybersecurity concerns extend to any software-based component, and train control HMIs are no different. Modern products have native cybersecurity mechanisms such as TPM modules and secure boot processes. They are fit for deployment in the most stringent cybersecurity environments.
The historical objections to software-based train control HMIs have been overcome. Indeed, 2023 will see the first fully touchscreen train control HMIs enter revenue service in the United States in a major mass transit system. Several other projects are in the delivery stages and will be commissioned in the next years. Operators can expect the technology to continue to be deployed.
Innovations continue of course. The emerging technologies, presented at the Innotrans Trade Show in Berlin in September 2022, include a Heads-Up Display (HUD) for train control systems. These systems – currently being deployed in automobiles and heavy haul equipment – project images in the line of sight of operators, either directly on a windshield or on a transparent screen called a combiner. The advantages of HUD technologies are that critical information can be communicated without the operator having to take their eyes off of the operational field of view. Current speed, for example, can be seen without looking down or away and is projected into a field of view, which appears some distance in front of the train.
As electronic train control screens and HUD technologies are introduced into the field of train control, they will reduce costs, increase operator efficiency and comfort and, ultimately, support a better and safer experience for the traveling public.
----------------
Blake Kozol is CEO of DEUTA AMERICA, Corp.
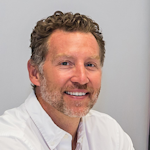
Blake Kozol | CEO, DEUTA AMERICA Corp.
Blake Kozol is CEO of DEUTA AMERICA, Corp., an international supplier of electronic systems installed inside freight and passenger cars.