Change is never easy. During a time of crisis, change needs to happen – and fast. Over the past two months, in response to the COVID-19 pandemic, hundreds of transit agencies throughout North America have risen to the challenge by adjusting maintenance practices to better protect riders, operators and maintenance staff. To reinforce system safety, transit maintenance departments have undertaken two major initiatives: adjusting cleaning protocols and undertaking special campaigns.
To learn more about these changes, Trapeze conducted an industry survey from March 27 – April 4, with 24 agencies responding. When asked the degree of impact COVID-19 has had on maintenance practices, 73 percent of participating agencies reported making “moderate to significant changes.” Thirteen percent reported no changes and 14 percent were not sure.
Adjustments to Cleaning Protocols
The types of cleaning changes made in the transit industry fall into the areas of frequency, procedures and safety protocols.
Cleaning procedures and frequency
Sixty-eight percent of agencies reported instituting additional cleaning procedures as a result of COVID-19. Specifically, agencies are focusing on doing a more thorough cleaning, with a special emphasis on sanitizing high-contact surfaces on vehicles, as well as at transit facilities (stations, stops, etc.).
Recently, WSP Canada created a report on public transit responses to COVID-19, creating a useful list of the high-contact surface areas in which to focus these increased cleaning efforts. The full list can be found here, but key vehicle surfaces include steering wheels, fareboxes, seats, door handles, exit buttons, handrails and poles. High-contact surfaces cleaned more often at transit facilities include kiosks, turnstiles, benches, railings, bike racks and restroom surfaces.
Not surprisingly, cleaning frequency has increased as a result of COVID-19, with 64 percent of respondents noting a change. Most agencies are disinfecting much more frequently such as after each trip, at the end of the alignment or hourly. Deep cleans vary from agency to agency. Some are deep cleaning more often (daily), while others are doing fewer deep cleans to focus time on more frequent contact-point cleaning. Off-cycle cleanings are happening on an as-needed basis for vehicles that carried a known COVID-19 infected operator or customer.
Cleaning products
It was a bit surprising that only 41 percent of participating agencies reported changing cleaning products by switching to stronger cleaning agents, disinfecting sprays and sanitizing wipes. Various commercial products, with powerful active ingredients including hydrogen peroxide, sodium hypochlorite and quaternary ammonium, are used to combat the virus throughout the industry.
For drivers and maintenance staff, hand sanitizers with at least 70 percent alcohol are frequently used. Disinfectant fogging or misting of vehicles, particularly any with a suspected COVID-19 positive passenger, is another common technique. For a detailed list of specific U.S. Environmental Protection Agency cleaning products that meet EPA’s criteria for use against SARS-CoV-2, see here.
Safety protocol adjustments
More frequent cleanings using stronger products has resulted in agencies taking additional measures to protect their staff. Sixty-four percent of agencies reported adjusting their safety protocols as a result of COVID-19. For frontline staff (cleaners, mechanics), there is a significant increase in the use of personal protective equipment. These changes make sense for the safety of staff who are using strong cleaning agents throughout the day.
To maintain social distance, agencies are reporting changes in how maintenance staff are interacting with each other in the workplace – changes in how they conduct meetings, training and work assignments. Survey respondents reported fewer in-person meetings, switching to remote learning (where possible) and limiting the number of mechanics and cleaners per shift.
Agencies are also leveraging their Enterprise Asset Management (EAM) systems more fully to maintain social distancing within the maintenance shop environment. Supervisors are assigning work to technicians within the system (without physical interaction). New cleaning procedure checklists are displayed to cleaners on-screen. Technicians and storekeepers can interact using the EAM system’s self-service features to request parts and tools, lookup vehicle history, etc.
Campaigns to protect drivers
Agencies are not just adjusting their cleaning protocols. They are also undertaking special vehicle and facility campaigns to further protect drivers and riders. Some of these projects are to encourage social distancing – i.e., removing or sectioning seats on vehicles. Others are installing signage at stations and stops to remind passengers to maintain at least six feet of distance.
These one-time projects involve maintenance retrofitting all buses. Installing plexiglass driver shields or changing the seat configuration to provide a safe buffer zone (no seats immediately behind the driver), are two examples. Figure 2 shows other common campaigns occurring in the industry.
Track it or it didn’t happen
Transit agencies report several ongoing challenges while adjusting workflow practices in response to COVID-19. Some agencies noted that staff are not taking the situation seriously enough, while others report staff struggling to track the cleanings they perform using the computer. Disregard for proper procedures can’t happen during a pandemic. The safety of staff and passengers depend on it. These are important issues that need to be addressed through additional training.
Equally important is to properly track all these new COVID-19 activities – cleaning protocols and maintenance campaigns – in your maintenance management system. Before the COVID-19 pandemic, Keolis Commuter Services (Boston) put together a change management campaign to ensure their staff correctly use their Trapeze asset management system. The company mounted posters throughout the maintenance facilities saying, “If it’s not in Trapeze, it never happened.”
This message has never been more important than it is right now. It is critical agencies track all new procedures in their asset management system of record to document all the good work agencies are performing. Doing so will give the general public the type of reassurance they need to rebuild transit ridership levels post COVID-19.
--------------------------------------------------------------------
Brett Koenig is the Industry Solutions Manager for the Trapeze Enterprise Asset Management (EAM) solution in use by more than 80 public transit organizations in North America.
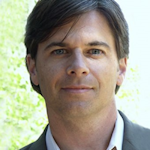
Brett Koenig | Industry Solutions Manager, Enterprise Asset Management
Brett Koenig is the Industry Solutions Manager for the Trapeze Enterprise Asset Management (EAM) solution in use by more than 80 public transit organizations in North America. Brett has 17 years of experience implementing public transit and rail asset management systems. As the Solutions Manager for EAM, Brett advises customers on industry trends and speaks at conferences about how a transit-focused EAM system can yield real-world efficiencies and measurable cost savings.