Going Vertical: The Upside of Multi-Level Transit Facilities
As transit agencies work with architects and engineers to build their projects, they not only need to address the project requirements within a budget but also must contend with project factors such as site constraints and regulations. Building a multi-level facility is one solution to these problems that entities including the Pioneer Valley Transit Authority (PVTA) and Connecticut Department of Transportation (CTDOT) have used to get the most out of their projects.
Site constraints
A great site is the foundation of every successful project. Transit agencies often struggle to acquire the best piece of land for their project due to key factors such as location, cost and adjacency to historic or protected properties, just to name a few. It is important for design teams to work closely with owners to make the most out of their site.
A great example of how site considerations can affect construction are newer, stricter stormwater retention requirements that were put in place to prevent detrimental soil erosion, stream contamination and other harmful environmental effects. These retention basins require substantial space on the site or can incur a significant cost impact if they are handled underground. Say you have the perfect site in mind for your facility: the right size, the right location, the right access. Yet you discover that the footprint of the building you had in mind would not leave enough space for the required retention basin. It isn’t time to start looking for a new site; it’s time to start rethinking the design of your facility.
Wetlands and floodplain regulations can also be a factor when building on a site. The Federal Transit Administration does not allow for building within the 100-year floodplain, while some insurers are even stricter. For instance, FM Global, who insures all state buildings in Connecticut, does not allow building within the 500-year floodplain. Rather than paying for large amounts of compacted fill to reach the 500-year floodplain, CTDOT chose to construct a ground floor level at the existing grade for employee car parking at their new Waterbury facility, and elevate the rest of the building to the 500-year level. This decision allowed them to have less impervious surface at grade level and protect views to the scenic mountains and rivers around the site.
A constrained site with limited access is another constraint that CTDOT was faced with when constructing their Waterbury facility. The chosen site is located within a valley between two mountains, with a river, a railroad and a recycling plant surrounding it. Site access is mostly restricted to one access point and there is not any available space to introduce new access roads. PVTA’s facility in Massachusetts had similar landlocked restrictions, with several industrial neighbors and a railroad locking it into having two access points from the same road. When dealing with this type of constraint, a thorough knowledge of factors such as bus circulation, fire department access, code compliance and parking requirements allows the design and stakeholder group to make critical decisions to make the most of each site challenge. In these cases, the entities’ willingness to take advantage of vertical space allowed them to better accommodate all of these factors within their chosen sites.
Finally, the most important reason to consider building up instead of out – looking to the future. It is essential not to use every available inch of the site in your initial design, which will be especially tempting on a site with space constraints. By spreading out over the site, all hope of future growth and expansion may vanish if adjacent property is unavailable. Both PVTA and CTDOT’s facilities, although working with similarly constrained sites, managed to leave ample room for growth on the south and north ends of their sites, respectively.
Debunking myths about construction expenses
By now the logistical benefits of building vertically should be plain and obvious, however, many owners believe that choosing a multiple level facility greatly increases cost. The truth is, when all site factors have been evaluated, going to a multi-level facility may be the most cost-effective option.
For instance, the foundation and mechanical systems of single and multi-level facilities are not fundamentally different. In fact, the necessary building height required for lifting buses lends itself to a second level that effectively makes use of the rest of that unused vertical space. Additionally, roof access convenience through the second floor can provide walkout access for ease of maintenance. In the cases of CTDOT and PVTA, the implementation of elevated administrative offices on a second level allows for a smaller building footprint on the site, the benefits of which have already been detailed.
Sustainable strategies that create workspaces people want to be in, such as daylighting, are another point in favor of multi-level facilities. Daylighting and exterior views are not possible from every workspace on a more spread out, single-level facility. However, the smaller footprint of a multi-level facility gives more opportunity for exterior views throughout the building. This benefits worker efficiency, employee retention and overall workplace satisfaction. For example, CTDOT’s Waterbury facility is designed to Connecticut’s High Performance Building Standard. The second floor allows for additional window frontage and views that give the offices a view of the outdoors. The maintenance bays similarly boast natural light and ventilation through an elevated clerestory.
Ultimately, the cost of building vertically is dependent on the size and scale of the facility and operation, and each case is unique. However, successes such as CTDOT and PVTA’s facilities show that going vertical can be not only viable but also preferable on sites with space, access or regulatory constraints.
-- -------
Sean Beachy, AIA, NCARB, serves as senior architect, senior associate principal for Wendel Companies.
Jeana Stright, RA, LEED AP, serves as architect, associate principal for Wendel Companies.
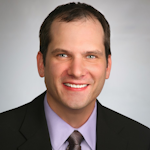
Sean Beachy
Sean Beachy AIA, NCARB, serves as senior architect, senior associate principal for Wendel Companies.
Jeana Stright | architect, associate principal
Jeana Stright, RA, LEED AP, serves as architect, associate principal for Wendel Companies.